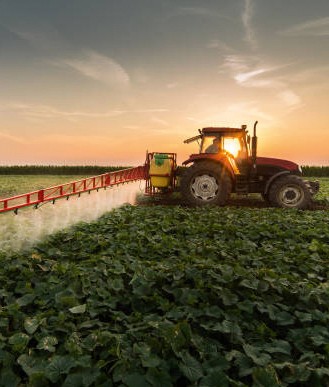
De plus en plus d'utilisateurs réfléchissent à l'intérêt ou à la possibilité de moduler les doses de produits phytosanitaires, ou de les réduire. Photo : Freeimages.com
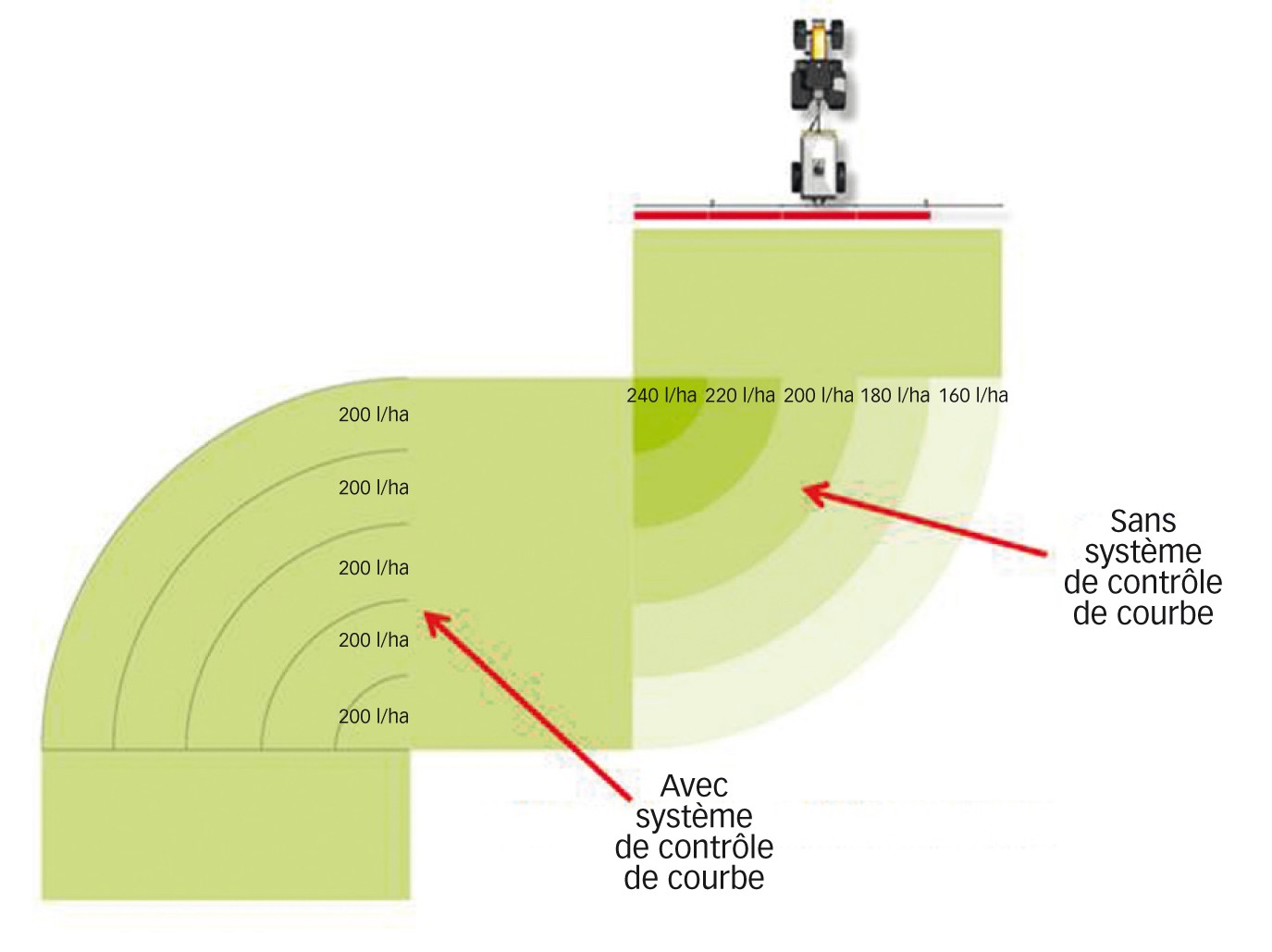
Fig. 1 : Effet d'un virage sur le non-respect de la dose (en l'absence de système de compensation) À noter que beaucoup de personnes utilisent le mot « dose » aussi bien lorsqu'ils parlent du produit de traitement que de la bouillie. Cet amalgame est d'autant plus facile à faire que la bouillie est un mélange à concentration constante d'eau et de produit (sauf pour les appareils à injection directe). Source : Mueller-Electonik
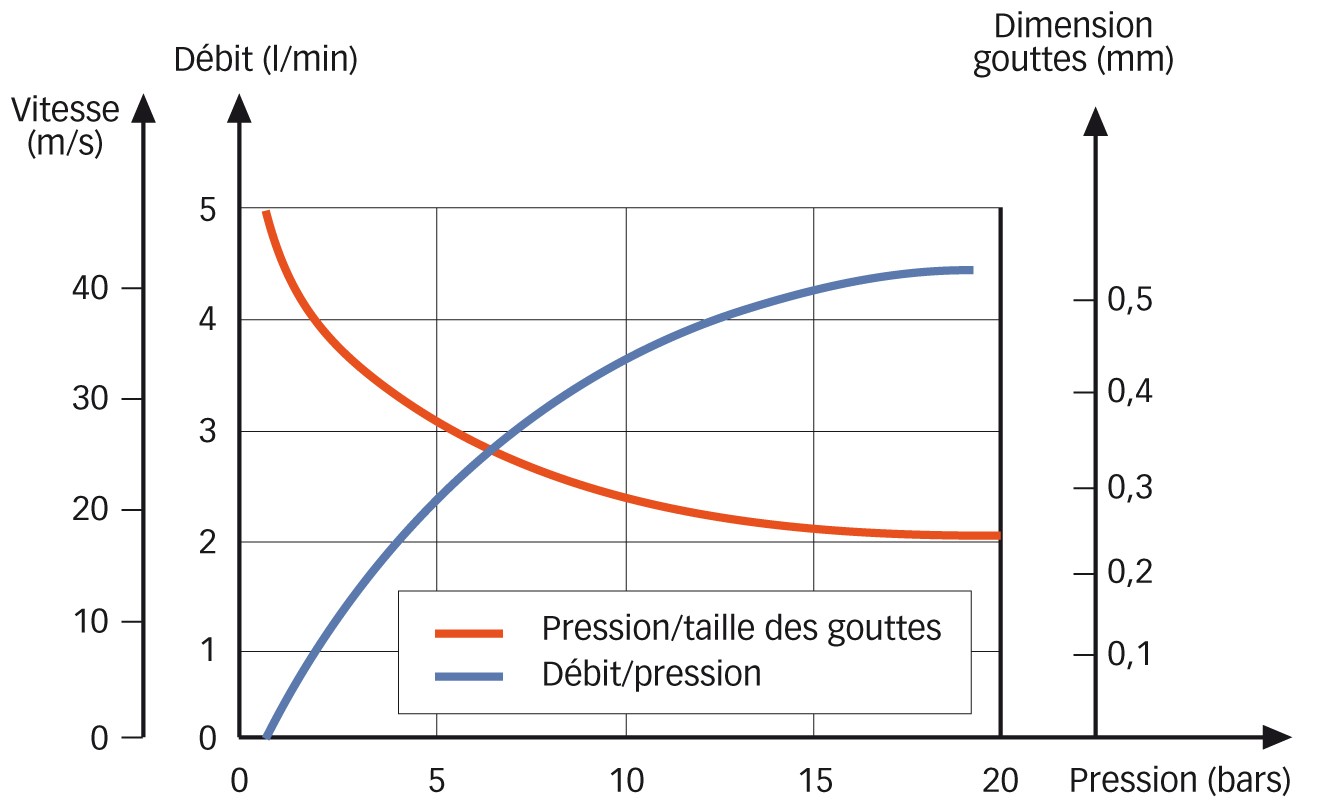
Fig. 2 : Relation débit/pression et relation pression/taille des gouttes Augmenter la pression peut amener assez rapidement à une taille trop faible des gouttes et donc générer une forte dérive. Source : Cemagref
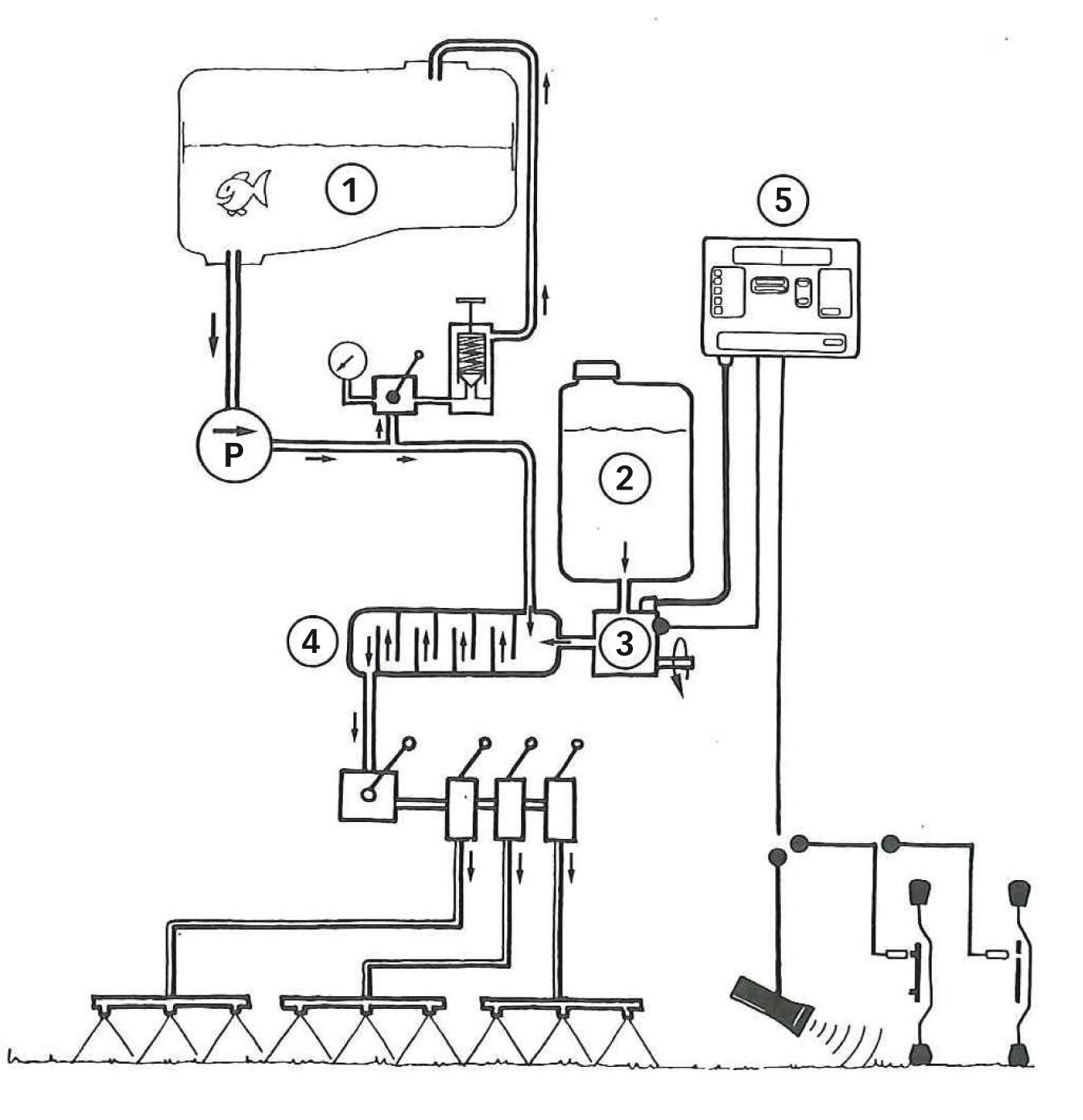
Fig. 3 : Principe d'un système à injection directe de type CPA (concentration proportionnelle à l'avancement) Cuve d'eau claire. Produit phytopharmaceutique dans son emballage d'origine. pompe doseuse. Mélangeur eau/produit. Boîtier de régulation CPA. Source : Arvalis-Institut du végétal
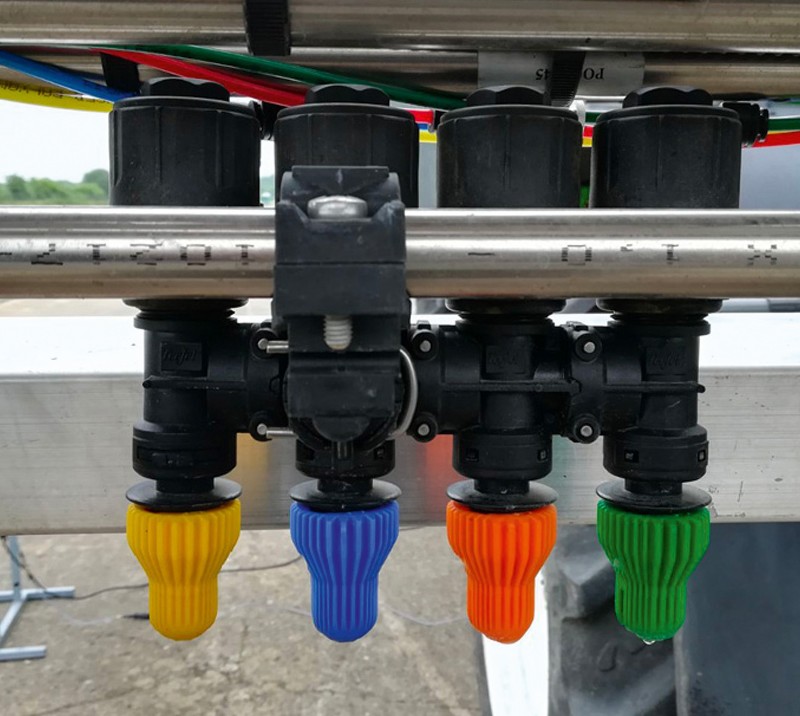
Q = (0 ou 1)* qi. Bloc porte-buses permettant d'obtenir des débits entre 0 et 15/8 q par incrément de 1/8 q (q = débit nominal). Photo : Tecnoma
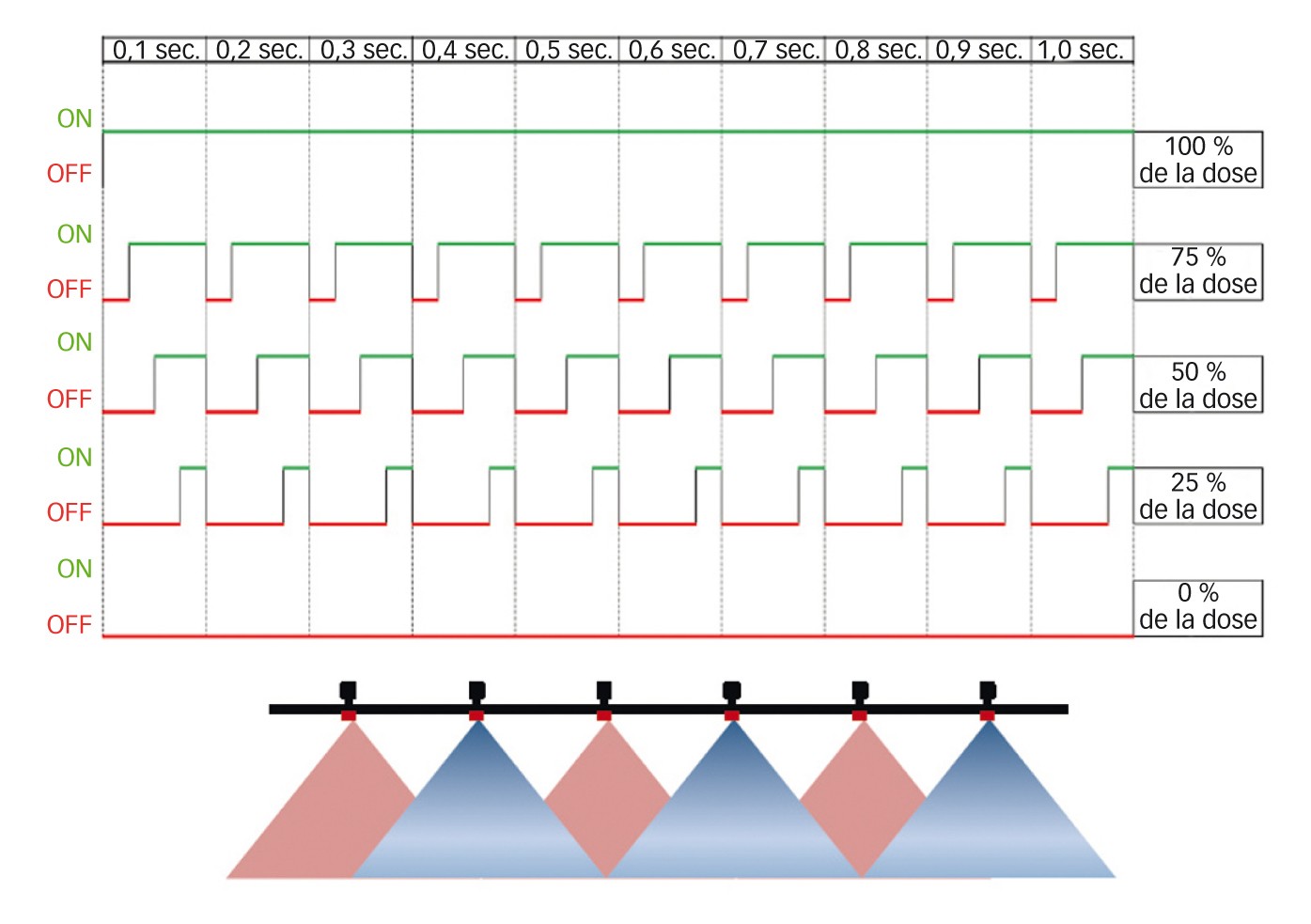
Fig. 4 : Principe de fonctionnement d'un système de buses à ouverture/fermeture rapides (commande de type PWM - Pulse Width Modulation) Source : Brian Finstrom, Capstan Ag, Inc.
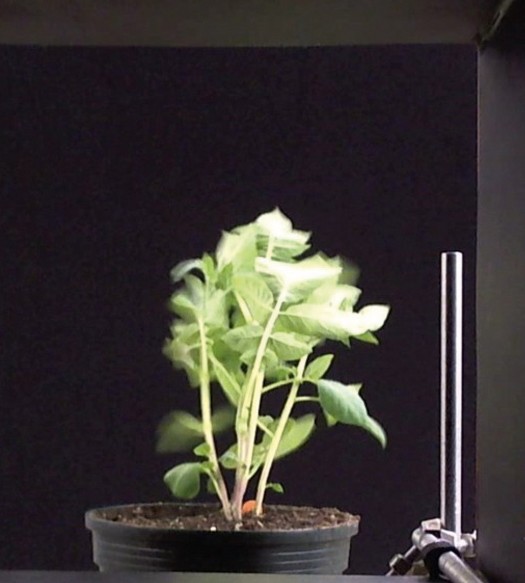
5. Ce plant est exposé à un vent de 18 km/h. Face à un vent modéré, les feuilles sont mises en mouvement, augmentant ainsi la possibilité de couverture par pulvérisation (image du centre), alors que pour un vent plus fort (image de droite), on constate un « effet de placage » des feuilles entre elles, entraînant une réduction de la couverture. Photos : B. Panneton - Agriculture and Agri-Food Canada
Pendant une trentaine d'années, nous avons eu tendance à considérer les dispositifs de régulation de type DPA (débit proportionnel à l'avancement) comme le summum en matière de qualité de la pulvérisation. Certes, ces dispositifs permettent d'obtenir la bonne dose à l'hectare (le volume de bouillie est apporté au litre près), mais cette excellence en matière de quantité apportée n'est pas pour autant synonyme de qualité de l'application. À l'heure où de nouvelles exigences s'imposent, à la fois en termes de réduction des doses et de modulation de ces doses, ainsi que de limitation des effets négatifs comme la dérive des produits, force est de constater que le DPA n'est pas l'outil qui convient. Ce système a - involontairement - contribué à ce que les utilisateurs oublient les fondamentaux de la pulvérisation. Et, d'une certaine façon, il a été la cause d'importantes erreurs de jugement de la part des professionnels.
Revenir aux fondamentaux de la pulvérisation
Dose moyenne et virages serrés
Les systèmes de régulation DPA permettent d'obtenir une dose à l'hectare précise, et ce, quelles que soient les variations de vitesse de l'ensemble tracteur/pulvérisateur. Que ces variations de vitesse soient intentionnelles ou non (accélérations ou décélérations en bout de champ, pentes, patinage du tracteur), le débit aux buses est ajusté en permanence de façon à ce que ces variations de vitesse soient sans effet sur la dose à l'hectare. Outre le grand confort de conduite que cela engendre, c'est aussi un élément clé dans la réduction drastique des volumes de fond de cuve puisqu'il est possible de préparer quasiment exactement la quantité de bouillie nécessaire au traitement d'une parcelle.
Pour autant, une régulation DPA n'est pas en soit synonyme de qualité de pulvérisation. La dose est certes respectée de façon stricte, mais il s'agit d'une dose moyenne. Le système DPA est en particulier pris en défaut dans le cas de virages serrés (Figure 1, page suivante) : une rampe - surtout si elle est de grande largeur (photo 1) - décrit une portion de cercle qui conduit à ce que les buses à l'intérieur du virage provoquent un surdosage du produit, alors que celles à l'extérieur vont le sous-doser. Il existe quelques systèmes qui limitent cet effet, mais le plus souvent il n'est pas pris en compte par les utilisateurs.
Une dose stricte permise par la variation de pression
L'aspect le plus préjudiciable du système DPA réside dans son principe même : maintenir strictement la dose nécessite de faire varier le débit instantané au niveau des buses ; cette variation de débit est obtenue par une action sur la pression de la bouillie au niveau de ces buses. Force est de constater que de nombreux professionnels, que ce soient des agriculteurs ou des techniciens, ont oublié la relation physique élémentaire qui relie ces deux variables :
- Q = k <221A>P avec Q = débit en m3/s, P = pression en Pascal ;
- k = coefficient de passage (constante liée à la forme de l'orifice calibré).
Ce qu'il faut retenir de cette équation qui lie le débit à la racine carrée de la pression, c'est que pour multiplier le débit instantané par deux, il faut multiplier la pression par quatre. Mais si on doit multiplier le débit par cinq, alors la pression devra être multipliée par vingt-cinq ! Tous les paramètres de la pulvérisation sont alors complètement modifiés, depuis la taille et le nombre de gouttes, en passant par l'angle du jet et les risques de dérive ou de ruissellement. Ce sont des situations que l'on rencontre couramment, en particulier en bout de champ, lorsqu'il faut passer d'une vitesse faible en raison des manoeuvres de demi-tour à une vitesse de travail qui est sensiblement plus élevée.
Moduler les doses... aux dépens de la qualité
De plus en plus d'utilisateurs réfléchissent à l'intérêt ou à la possibilité de moduler les doses de produits phytosanitaires, ou de les réduire. Ceci pose de nombreuses questions en ce qui concerne la qualité de la protection en cas de non-respect des doses homologuées, questions qui ne font pas l'objet de cet article. Mais cela pose aussi - et surtout - des questions quant à la faisabilité technique, c'est-à-dire à la capacité des appareils de pulvérisation actuels à être utilisés de cette manière, sans dégradation de la qualité de la pulvérisation. Car la solution qui est immédiatement envisagée est justement de faire varier la dose au sein de la parcelle en modifiant la pression de travail. Si une telle modulation des doses par variation de débit est possible, elle n'est en revanche pas du tout souhaitable car, comme indiqué dans le chapitre suivant, elle entraîne une dégradation des paramètres de pulvérisation.
La relation débit/pression au centre de la problématique
Une relation entre la pression, l'angle de jet et les gouttes
Les variations de pression ont comme répercussion une variation du débit, mais malheureusement ces variations de la pression vont également modifier de façon sensible d'autres paramètres de la pulvérisation qui sont autant d'éléments clés dans la réussite des traitements et/ou dans leur incidence sur l'environnement. Ainsi sont liés à la pression :
- l'angle du jet des buses, réduire la pression conduit à une diminution de l'angle du jet ;
- la taille des gouttelettes (Figure 2), augmenter la pression peut amener assez rapidement à une taille trop faible des gouttes et donc générer une forte dérive des produits ; à l'inverse, une diminution de la pression va augmenter la taille des gouttes et ainsi favoriser leur ruissellement au sol ;
- parallèlement à la taille des gouttelettes, la pression a une incidence forte sur le nombre de gouttelettes produites par unité de volume de bouillie (une gouttelette de 400 µm peut être fractionnée en huit gouttes de 200 µm, ou en 64 gouttes de 100 µm, le volume étant en relation avec le cube du diamètre) ;
- la variation de la taille des gouttes va également modifier leurs caractéristiques en matière de vitesse limite, de dessèchement dans l'air, de transport par le vent, de pénétration dans le feuillage...
Fixer et conserver les critères de qualité
La recherche de la meilleure qualité de pulvérisation est donc un compromis judicieux entre des critères qui sont pour certains antagonistes entre eux. Il faut définir ces critères de façon cohérente selon la qualité recherchée, et à partir de là conserver ces critères coûte que coûte !
Le premier critère à fixer est la taille des gouttes : ces dernières ne doivent être ni trop fines ni trop grosses. La fourchette souvent préconisée en termes de VMD (diamètre volumique moyen) se situe entre 200 et 300 µm (250 à 350 µm selon d'autres sources), et ce diamètre doit être déterminé en fonction de paramètres comme le stade de la culture, le type de produit et son mode d'action...
Le dilemme à résoudre si on veut moduler les doses de produits peut se résumer ainsi : comment faire varier la dose sans faire varier d'un iota la pression de travail, c'est-à-dire sans dégrader de quelque manière que ce soit la qualité de l'application ?
La technologie au secours de la qualité de l'application
Travailler à pression constante
Le découplage de la formule liant débit et pression ne peut s'effectuer qu'au prix d'astuces et d'innovations, mais de nombreuses solutions existent et sont disponibles sur le marché (et pour certaines d'entre elles, depuis plus de trente ans). Elles reposent notamment sur un des trois principes suivants.
La première solution consiste à ne pas faire varier le débit aux niveaux des buses, et donc à travailler à pression constante et à volume d'eau par hectare constant. Pour faire varier la dose il faut alors faire varier la concentration du produit dans la bouillie. C'est ce que l'on trouve sur les appareils à injection directe, pour lesquels il n'y a pas de mélange préalable du produit dans la cuve : le mélange s'effectue au plus près des buses (Figure 3). Et ce mélange - la concentration du produit dans l'eau - peut être modulé tout au long du travail de pulvérisation, le volume de bouillie quant à lui ne varie que de façon infime.
Ce système est utilisé notamment aux États-Unis depuis une trentaine d'années pour la modulation des doses d'herbicides sur maïs ou soja. Les précurseurs sont les entreprises Raven et John Deere. En Europe, il existe plusieurs mises en oeuvre de ce type, comme en France celle de Dosatron International depuis les années 1980, ou plus récemment le projet PiiX de Diimotion, qui est un bloc d'injection directe de produits solides et/ou liquides pour les appareils utilisés en viticulture.
Le principal défaut de l'injection directe est son manque de réactivité face aux variations rapides de la vitesse du tracteur. Il y a un retard de plusieurs secondes (donc de plusieurs mètres parcourus) entre la prise en compte d'une nouvelle vitesse et l'arrivée de la nouvelle concentration de produit à la buse. L'injection directe est donc adaptée à la modulation des doses de produits pour autant que cette modulation puisse être anticipée.
Ce dispositif simplifie également la logistique induite par la préparation des bouillies : pas d'allers-retours à l'exploitation pour réapprovisionner la cuve, pas de temps de préparation de la bouillie. C'est donc une voie prometteuse pour un plus grand respect des créneaux climatiques favorisant une pulvérisation de qualité.
Modifier le nombre et/ou le type de buses
La deuxième voie de découplage « débit-pression » consiste à modifier le nombre et/ou le type de buses utilisé. Pour modifier le débit tout en conservant la pression adaptée à la qualité recherchée, on utilise des blocs porte-buses équipés de trois ou quatre buses aux caractéristiques différentes (photo 2), par exemple une buse avec un débit nominal q, une autre dont le débit à la même pression est de q/2, une autre avec q/4 et une dernière avec q/8. Dans cet exemple, la sélection de la buse et/ou l'ouverture simultanée de plusieurs de ces buses permet d'obtenir tous les débits entre 0 (toutes les buses sont fermées) à 15/8 x q lorsque les quatre buses sont ouvertes, soit quasiment 2 q. La variation de débit se fait ici par incrément de q/8, avec seize possibilités différentes de débit pour une pression qui reste inchangée.
Ce système commercialisé par plusieurs sociétés (John Deere, Lechler...) est utilisable pour répondre à des problématiques de variation de vitesse du fait de sa forte réactivité, et également à des fins de modulation des doses de produit, c'est-à-dire pour pouvoir travailler au quart, à la moitié... de la dose préconisée dans certaines zones de la parcelle, et de travailler à la dose préconisée à d'autres endroits. Il est envisageable de moduler les doses bloc par bloc, et par exemple de conserver la même dose entre l'intérieur et l'extérieur d'un virage serré.
Ouverture/fermeture des buses
Une troisième solution consiste à n'utiliser qu'une seule buse, mais à faire en sorte que le débit de cette buse soit modulé sans pour autant toucher à la pression de travail. Le principe utilisé est le pilotage de l'ouverture/fermeture de ces buses au moyen d'électrovannes rapides. L'ouverture et la fermeture des buses alternent à des cadences de dix, voire vingt fois par seconde. Le débit instantané résulte de la proportion respective des temps d'ouverture par rapport aux temps de fermeture, ce que l'on nomme le rapport cyclique. On parle également de PWM (Pulse Width Modulation ou modulation de la largeur d'impulsion) (Figure 4).
La modulation du débit peut se faire buse par buse, ce qui permet de respecter la bonne dose en toute situation, comme dans le cas de virages serrés avec un pulvérisateur à rampe large. Ce dispositif est aussi tout à fait adapté à la modulation des doses de produit selon les besoins de la culture en chaque endroit de la parcelle (création de zones intraparcellaires). Sur des pulvérisateurs viticoles par exemple, il permet aussi de moduler la dose selon l'étage foliaire (protection renforcée de la zone de grappes par rapport à la zone des feuilles, ou inversement), ou selon la densité de la canopée, voire l'absence de feuillage (arrêt de la pulvérisation en cas de « trous de végétation »).
Respecter la qualité de l'application
D'une dose/hectare à une posologie
La volonté de moduler les doses de produits phytosanitaires a le mérite de remettre en lumière des aspects techniques facilement oubliés, et de moins en moins enseignés, qui mériteraient d'être beaucoup plus intégrés à la formation pour l'obtention du certiphyto.
Les technologies pour moduler les doses de produits sont disponibles sur le marché, mais leur usage nécessite d'en comprendre le fonctionnement et - surtout - de changer l'approche méthodologique en termes de réglage du pulvérisateur. Il serait intéressant de dépasser la notion de dose à l'hectare, pour passer à une approche basée sur la qualité de l'application et sur une notion de « posologie » (par exemple, une posologie exprimée en µg de produit par cm²).
Deux critères : diamètre des gouttes et nombre d'impacts
Le premier paramètre à fixer est le diamètre des gouttelettes optimal au regard du produit et de la cible (de façon courante, ce diamètre sera compris dans une « fourchette idéale » allant de 200 µm à 350 µm). Ce faisant, les risques de ruissellement au sol et les risques de dérive sont limités. Concernant ces derniers, il semble plus cohérent de limiter « à la source » les phénomènes de dérive, plutôt que d'essayer de les atténuer avec des dispositifs compliqués à utiliser, comme les panneaux récupérateurs. Ces panneaux permettent de récupérer une bonne partie de la dérive, mais pour autant l'application réalisée est-elle optimale ? Ne faudrait-il pas que toutes les gouttes générées par l'appareil soient captées par les cibles, c'est-à-dire le feuillage le plus souvent au lieu d'être recyclées ?
Un second aspect à considérer est le nombre d'impacts par cm². Selon les produits, leur mode d'action (contact ou systémique) et le type de cible, il est recommandé d'obtenir entre 20 et 70 gouttes/cm². En choisissant une taille de gouttes comprise dans la « fourchette idéale », et même en se fixant comme seuil minimal d'avoir 50 gouttes/cm², cet objectif est facilement atteignable, y compris avec des applications à bas volume (tableau ci-dessus).
Vers une pulvérisation sélective
Les trois systèmes innovants présentés ci-dessus (injection directe, bloc multibuses et buses pilotées par PWM) permettent à la fois d'assurer une qualité d'application et de moduler les doses de produits. Leurs caractéristiques diffèrent, en particulier en matière de réactivité. Il est possible de les associer afin de tirer le meilleur parti de chaque système (par exemple associer l'injection directe et les buses PWM).
Non seulement ces innovations sont la clé pour améliorer sensiblement la qualité des applications de produits, mais elles ouvrent des perspectives en matière de modulation de doses et également en matière de pulvérisation sélective ». Depuis de nombreuses années, chercheurs et industriels travaillent sur ce sujet, dans l'objectif d'adapter la pulvérisation soit à l'absence/présence de végétation, soit à la quantité de biomasse présente. Parmi les applications connues, le Weedseeker, commercialisé dès 2001 détecte la végétation dans un environnement censé ne pas en avoir (repousses sur chaume, herbes sur voies ferrées...). Le système de détection est basé sur les différences de réflectance dans le rouge et l'infrarouge de la végétation d'une part, et des corps inertes (sol, chaumes...) d'autre part. Avidor Hightech proposait durant les années 2010, avant sa cessation d'activité, un système sur pulvérisateur arboricole qui interrompait la pulvérisation entre deux arbres, grâce à un capteur à ultrasons qui « captait » le trou de végétation. Diimotion propose le système Smac (médaillé au dernier salon virtuel Vinitech), qui permet la coupure automatique de la pulvérisation en l'absence de feuillage (pas de vigne, pas de spray). Le système est composé de trois ou quatre capteurs à ultrasons par demi-face, et de trois ou quatre électrovannes associées à ces capteurs. La coupure de la pulvérisation est donc modulée sur la hauteur de la végétation, et non pas par tronçons entiers.
Grâce au développement de nouveaux capteurs plus sophistiqués que les capteurs à ultrasons (caméras hyperspectrales, Lidar...), les pulvérisateurs seront capables de reconnaître les adventices et donc d'appliquer l'herbicide adapté, ou encore de moduler la dose de produit en fonction de la quantité de biomasse.
Des marges de progrès importantes
Il reste encore des marges de progrès importantes en matière de qualité de l'application. Elles concernent essentiellement les appareils à jet porté. Objectivement, on manque de données fiables en ce qui concerne les caractéristiques optimales des flux d'air (photos 3 à 5) : vitesse, angle des jets...
Le problème des nuisances sonores des appareils à jet porté est certainement un aspect important, bien que peu pris en compte pour le moment. Le bruit généré par la turbine centrale est très important, et il est potentiellement source de conflits de voisinage. Alors que l'utilisation de pulvérisateurs dans les champs, les vignes et les vergers est de moins en moins bien tolérée par le grand public, il serait bon d'innover très rapidement en matière de matériels à jet porté. Les innovations devraient porter en priorité sur l'amélioration de la qualité de la protection phytosanitaire, par une meilleure maîtrise des paramètres de pénétration dans le feuillage, de mise en mouvement de la végétation...
Mais ces innovations doivent aller également dans le sens d'une réduction drastique du bruit des pulvérisateurs à jet porté, probablement par l'abandon des grosses turbines centrales au profit de plusieurs micro-turbines disposées au plus près des buses. Cette disposition devrait permettre de réduire les nuisances sonores, tout en réduisant les différences de pression et de vitesse d'air liées aux pertes de charge entre turbine et sorties d'air.
Et cette évolution est tout à fait en phase avec la généralisation de motorisations électriques - en particulier sur les tracteurs électriques -, motorisations électriques qui amènent de nouvelles possibilités comme la modulation des flux d'air au niveau de chaque sortie.
RÉSUMÉ
CONTEXTE - Ajuster la dose de produit appliqué peut répondre à plusieurs contraintes : la variation de la vitesse d'avancement, le développement de la surface foliaire à traiter... Toutefois, cet ajustement doit impérativement être envisagé en respectant les conditions optimales d'application, lesquelles reposent sur quelques principes de base.
PROBLÉMATIQUE - Pour modifier la dose, le premier réflexe consiste à varier le débit. Or la relation débit/pression est au centre de la problématique de la qualité de la pulvérisation, la variation de pression modifiant l'angle de jet de la buse et la formation des gouttes. Il faut donc pouvoir varier la dose sans modifier la pression de travail.
TECHNOLOGIES - Des solutions performantes permettent d'ajuster les doses sans modifier la pression et sans dégrader ainsi la qualité de la pulvérisation. Elles reposent sur trois technologies : l'injection directe, les blocs porte-buses, l'ouverture-fermeture séquencée des buses.
MOTS-CLÉS - Pulvérisation, dose, modulation, ajustement, débit, pression, gouttes.
POUR EN SAVOIR PLUS
CONTACT : gilbert.grenier@agro-bordeaux.fr
LIENS UTILES : https://tinyurl.com/y2dklguu
https://tinyurl.com/y43v9pbh
https://tinyurl.com/y44wpnln
- Sidahmed M. M., 1996. A theory for predicting the size and velocity of droplets from pressure nozzles. Trans. Asae 40(3):547-554.
- Schick R., 1997. An engineer's practical guide to drop size,Wheaton, Ill.: Spraying Systems Co.
- Ozkan H. E., 1998. Effects of major variables on drift distances of spray droplets, FactSheet AEX 525-98. Columbus, Ohio: Ohio State University Extension.
- Panneton B., Piché M., 2005. Interaction between application volume, airflow, and spray quality in air-assisted spraying.Trans. Asae 48(1): 37-44.
- Nuyttens D., Baetens K., De Schampheleire M., Sonck B., 2007. Effect of nozzle type, size, and pressure on spray droplet characteristics. Biosystems Eng. 97(3): 333-345.
- Kooij S., Sijs R., Denn M. MM, Villermaux E. , Bonn D., 2018. What determines the drop size in sprays? Physical Review X8,031019.